- Understanding Inventory Management
- Importance of Inventory Control
- Types of Inventory
- Techniques for Inventory Valuation
- FIFO (First-In, First-Out) Method
- LIFO (Last-In, First-Out) Method
- Inventory Costing Methods
- Specific Identification Method
- Weighted Average Method
- Inventory Management Strategies
- Just-In-Time (JIT) Inventory System
- ABC (Activity-Based Costing) Analysis
- Conclusion:
Students pursuing studies in accounting often encounter challenges in comprehending the profound significance of inventory management in the realm of managerial accounting. The intricate nature of this facet often poses a hurdle, demanding a comprehensive understanding to navigate the complexities of financial management effectively. This blog endeavors to bridge this gap by offering an in-depth and exhaustive overview, positioning itself as a steadfast companion for students as they delve into this critical dimension of financial oversight. If you need help with your managerial accounting assignment, I'm here to provide expert assistance and support to ensure your success in mastering the intricacies of inventory management within the realm of managerial accounting.
Inventory management stands as a cornerstone in the discipline of managerial accounting, wielding immense influence on a company's financial health and operational efficiency. At its core, it encompasses a series of methodologies, principles, and strategies essential for overseeing and controlling a company's inventory. Yet, grasping the subtleties of these concepts demands meticulous exploration and clarity, particularly for budding accounting professionals aiming to establish a solid foundation in this field.
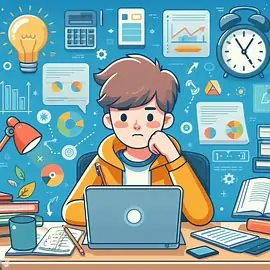
The journey into understanding inventory management within the purview of managerial accounting requires a multifaceted approach. It involves unraveling the intricacies of inventory control systems, valuing inventory using distinct methods, comprehending cost flows, and adopting strategic approaches to optimize inventory management processes.
This blog endeavors to unravel the complexities surrounding inventory management by shedding light on its multifaceted components. It seeks to demystify the challenges that students often encounter while navigating through topics such as inventory valuation, costing methods, inventory control strategies, and the interplay of these elements within the broader scope of financial decision-making.
By serving as a comprehensive guide, this blog aims to equip students with the requisite knowledge, tools, and perspectives essential for comprehending inventory management in managerial accounting. It seeks to empower them to make informed judgments and strategic choices when confronted with real-world scenarios in their academic pursuits and future professional endeavors.
In essence, this blog endeavors to be a beacon of clarity and understanding, guiding students through the labyrinth of inventory management intricacies, ensuring they emerge well-versed and confident in their grasp of this indispensable facet of accounting and financial management.
Understanding Inventory Management
To comprehend the fabric of inventory management is to unravel the very essence of its role within managerial accounting. This facet represents more than mere stockpiling; it embodies a systematic orchestration of resources that profoundly influences a company's financial well-being.
Inventory management encapsulates a spectrum of practices aimed at optimizing the balance between supply and demand. It involves the strategic administration of goods, encompassing their procurement, storage, tracking, and eventual utilization or sale. At its core, this discipline seeks to strike a delicate equilibrium between maintaining adequate inventory levels to meet customer demand and minimizing excessive holding costs that might impede profitability.
Within the ambit of managerial accounting, understanding inventory management necessitates a deep dive into the intricacies of cost control, efficient utilization of resources, and the holistic impact on financial statements. It demands an appreciation of various inventory valuation methods, the significance of inventory turnover, and the underlying principles guiding inventory control systems.
Therefore, comprehending inventory management isn't merely about tallying stocks; it's about orchestrating a symphony of financial prudence, operational efficiency, and strategic decision-making—all vital components in steering the success of any organization.
Importance of Inventory Control
The cornerstone of financial success for any business lies in mastering effective inventory control. It represents the linchpin in the delicate balancing act between supply and demand, directly impacting a company's bottom line. Effective inventory control ensures a company maintains optimal stock levels, preventing overstocking that ties up valuable resources or understocking that leads to lost sales opportunities.
By implementing sound inventory control measures, businesses can streamline operations, minimize carrying costs, and enhance cash flow. Moreover, it aids in meeting customer demands promptly, bolstering customer satisfaction and loyalty. The ripple effect of efficient inventory control extends to improving financial ratios, such as inventory turnover and return on investment, thereby strengthening the overall financial performance of an organization.
In essence, the significance of inventory control in optimizing financial performance cannot be overstated. It stands as a linchpin, wielding considerable influence on a company's profitability, operational efficiency, and customer-centricity.
Types of Inventory
Understanding the nuances of inventory in managerial accounting entails recognizing its diverse categories and their pivotal roles in the financial landscape. Inventories manifest in various forms, each bearing its unique characteristics and significance.
Raw materials comprise the foundational inventory category, encompassing the basic components used in the production process. Work-in-progress inventory encapsulates goods in various stages of production, representing an integral part of the manufacturing cycle. Finished goods inventory, the final product awaiting distribution or sale, holds paramount importance in meeting customer demands.
Furthermore, understanding merchandise inventory is crucial for businesses involved in buying and selling tangible goods. This inventory class typically includes products ready for sale in retail or wholesale settings.
Acknowledging these diverse inventory types is essential in managerial accounting as it enables accurate financial reporting, aids in strategic decision-making, and facilitates efficient inventory management tailored to each category's specific characteristics and requirements.
Techniques for Inventory Valuation
Mastering inventory valuation techniques stands as a pivotal aspect within managerial accounting, influencing financial statements and strategic decision-making. Two primary methods, FIFO (First-In, First-Out) and LIFO (Last-In, First-Out), dominate this sphere.
The FIFO method attributes the costs of the earliest inventory acquired to goods sold first, mirroring the chronological flow of inventory. It tends to reflect current market prices more accurately during inflationary periods, potentially resulting in higher reported profits and lower tax burdens.
Conversely, the LIFO method assigns the costs of the most recent inventory purchases to goods sold, assuming that the latest items added to inventory are the first to be sold. LIFO often results in lower taxable income during inflationary periods due to higher cost of goods sold, but it might not truly represent the physical flow of inventory.
Both methods possess distinct advantages and drawbacks, influencing financial ratios, tax liabilities, and net income. However, their significance extends beyond mere numbers; they offer insight into inventory management strategies and their implications on financial reporting.
Understanding these valuation methods within managerial accounting empowers businesses to make informed decisions, navigate tax implications, and accurately represent inventory value on financial statements, ensuring a clearer depiction of a company's financial standing.
FIFO (First-In, First-Out) Method
The FIFO method, a cornerstone in inventory valuation, operates on the principle that the first inventory items purchased are the first to be sold or used. This approach mirrors the physical flow of goods, attributing the costs of the earliest inventory purchases to goods sold or transferred out of inventory.
In practical terms, during times of rising prices, FIFO tends to result in a higher valuation of ending inventory, as the cost of goods sold reflects older, lower-priced inventory. This leads to increased reported profits and lower taxable income due to the matching of lower costs against current revenues.
By adhering to the chronological order of inventory flow, the FIFO method offers businesses an approach that often aligns with the actual movement of goods. However, its impact on financial reporting requires careful consideration, especially concerning its potential to overstate profitability during inflationary periods. Understanding and applying the FIFO method aids in providing a more accurate representation of inventory value and financial performance within managerial accounting contexts.
LIFO (Last-In, First-Out) Method
The LIFO method, a prominent inventory valuation technique, operates on the premise that the most recently acquired inventory items are the first to be sold or utilized. This approach contrasts with FIFO, reflecting the assumption that newer inventory costs are matched against revenue.
In practical terms, during inflationary periods, LIFO typically results in a lower valuation of ending inventory, as the cost of goods sold comprises the higher-priced recent inventory. Consequently, reported profits tend to decrease, leading to higher tax deductions due to the matching of higher costs against revenues.
While LIFO may better represent the current cost of goods sold, its use can present challenges in accurately reflecting the actual flow of inventory. Moreover, it may potentially understate the value of ending inventory, impacting financial ratios and tax liabilities. Understanding the nuances of the LIFO method is crucial in managerial accounting, as it influences inventory valuation methods and financial statements, shaping a company's reported financial standing and tax obligations.
Inventory Costing Methods
Inventory costing methods play a fundamental role in determining the value of goods held by a company, directly impacting financial statements and managerial decision-making. Two primary techniques—Specific Identification and Weighted Average—offer distinct approaches to assigning costs to inventory items.
The Specific Identification method uniquely identifies and assigns the actual cost of each individual inventory item. This method is particularly suitable for businesses dealing with high-value or distinct items, allowing precise tracking of costs and valuation based on specific purchase prices.
In contrast, the Weighted Average method calculates the average cost per unit based on both the cost of goods available for sale and the quantity of goods. This approach provides a blended cost for inventory items, offering simplicity in calculation and a smoother reflection of costs amidst price fluctuations.
Both methods present advantages and limitations. While Specific Identification offers accuracy, it might not be feasible for inventories comprising numerous identical items. Conversely, the Weighted Average method provides a uniform cost but might mask variations in individual item costs.
Understanding these inventory costing methods is crucial for managerial accountants, as they dictate how inventory costs are allocated, impacting financial reporting, tax obligations, and managerial decision-making processes. Grasping the nuances of each method enables informed choices aligning with a company's operational needs and financial objectives.
Specific Identification Method
The Specific Identification method stands as a meticulous inventory costing technique that uniquely assigns actual costs to individual inventory items. Particularly valuable for businesses dealing with distinct or high-value items, this method allows for precise tracking and valuation based on specific purchase prices for each item.
In essence, this method involves directly linking the actual cost of each inventory unit to its sale or usage. It is highly suitable for products with identifiable and distinguishable characteristics, enabling accurate matching of costs with revenues for those specific items.
While offering unparalleled precision in valuing unique inventory items, the Specific Identification method may not be practical for inventories comprising numerous identical items. Implementation complexities and administrative burdens arise when each unit requires individual tracking and identification, potentially rendering this method less feasible for inventories with high volume or homogeneous items. Understanding the intricacies of the Specific Identification method is crucial for businesses seeking precise valuation and cost matching for specific inventory items within their accounting and financial management practices.
Weighted Average Method
The Weighted Average method represents an inventory costing approach that calculates the average cost per unit by considering both the total cost of goods available for sale and the total quantity of goods. This method provides a blended cost for inventory items, irrespective of fluctuating purchase prices.
By dividing the total cost of available goods by the total number of units, the Weighted Average method offers a uniform cost per unit. It simplifies the valuation process, providing a middle-ground cost figure that smoothens out price variations and simplifies cost calculation.
This method proves advantageous in scenarios where individual item costs are challenging to trace or when dealing with homogenous inventory items. However, its simplicity might obscure specific cost fluctuations, potentially leading to less precise cost allocations compared to the Specific Identification method.
Understanding the Weighted Average method is imperative for businesses seeking a straightforward inventory costing approach that balances cost precision with administrative ease, thereby facilitating efficient financial reporting and informed decision-making in managerial accounting contexts.
Inventory Management Strategies
It is needed for production or sale, this strategy reduces storage costs, minimizes waste, and enhances operational efficiency. However, it necessitates robust supplier relationships and impeccable logistical coordination to mitigate supply chain risks.
On the other hand, ABC Analysis categorizes inventory items based on their significance, allocating resources and attention to items with the highest value or impact on business operations. This strategy helps prioritize inventory management efforts, channeling resources where they yield maximum benefit, and optimizing inventory control. Nonetheless, it requires meticulous data analysis and ongoing evaluation to remain effective.
Understanding and implementing these inventory management strategies are pivotal for businesses striving to strike a balance between meeting customer demands, minimizing costs, and maximizing profitability. Mastery of these strategies empowers businesses to streamline processes, mitigate risks, and bolster financial performance within the realm of managerial accounting.
Just-In-Time (JIT) Inventory System
The Just-In-Time (JIT) Inventory System represents a lean inventory management strategy focused on minimizing inventory levels to match production or sales demands precisely. This approach aims to eliminate excess inventory holding costs while ensuring goods arrive precisely when needed.
By synchronizing production with demand, the JIT system reduces warehousing expenses, carrying costs, and the risk of obsolete inventory. Additionally, it streamlines production processes, leading to improved operational efficiency and reduced lead times.
The impact of JIT on cost reduction and operational efficiency is substantial. Lower inventory holding costs and minimized waste contribute to overall cost reduction, while enhanced efficiency in production and logistics leads to smoother operations and improved responsiveness to customer demands. However, the successful implementation of JIT requires robust supply chain management, reliable suppliers, and stringent quality control to mitigate potential risks associated with lean inventory levels. Understanding and implementing JIT principles can significantly benefit businesses aiming to streamline operations and achieve cost-effective inventory management.
ABC (Activity-Based Costing) Analysis
ABC (Activity-Based Costing) Analysis involves categorizing inventory items based on their significance in relation to business operations. This method recognizes that not all inventory items contribute equally to the company's overall success, hence the need for a prioritization strategy.
The ABC analysis classifies inventory items into categories (A, B, and C) based on their value, usage frequency, or impact on operational processes. Category A typically includes high-value items or those critical to operations, demanding meticulous attention and management. Category B comprises items of moderate importance, while Category C involves lower-value items or those with minimal impact on operations.
By categorizing inventory items in this manner, businesses can allocate resources, time, and focus according to the items' significance. Category A items may receive closer monitoring, while Category C items might require less frequent oversight.
Implementing ABC Analysis aids in prioritizing inventory management efforts, optimizing resources, and ensuring efficient allocation of time and attention to inventory items that significantly influence operational efficiency and financial performance. Understanding and applying this analysis empowers businesses to streamline inventory control and make informed decisions within managerial accounting contexts.
Conclusion:
In conclusion, the world of inventory management within managerial accounting is a multifaceted realm that demands intricate understanding and strategic application. Throughout this blog, we've explored the fundamental aspects crucial for students navigating this intricate landscape.
From comprehending inventory management's significance in financial health to delving into various techniques and strategies, this exploration aimed to equip students with a foundational understanding. Inventory control emerged as a linchpin, directly influencing a company's financial performance, operational efficiency, and customer satisfaction.
We dissected inventory valuation methods like FIFO and LIFO, highlighting their distinct impacts on financial statements and decision-making processes. Similarly, inventory costing methods such as Specific Identification and Weighted Average were elucidated, emphasizing their precision and applicability based on inventory characteristics.
Moreover, we delved into strategic approaches like the JIT Inventory System and ABC Analysis, showcasing their pivotal roles in cost reduction, operational efficiency, and resource optimization.
Understanding these nuances empowers students to steer through complex managerial accounting scenarios, make informed decisions, and contribute meaningfully to organizational success. By grasping the intricacies of inventory management, students can embark on a journey towards becoming adept financial professionals capable of navigating the intricate interplay between inventory, accounting, and business success. Embracing these principles will undoubtedly serve as a compass guiding students in their educational pursuits and future endeavors within the realm of accounting and finance.